Freyssinet invented the individually-protected multi-strand stay cable and is the world leader in bridge stay cables, having completed over 400 structures. Freyssinet stay cables are a benchmark in terms of fatigue resistance, corrosion protection, ease of inspection and ease of replacement. Somnath Biswas, Managing Director, Freyssinet Menard India Pvt. Ltd, tells us more about this technology.
The specifications of the stay cable system shall comply with supply, testing and permanent protection of the stay cables. It includes the stay components which are part of the structure, such as the formwork tubes/pipes, the anchorage bearing plates, erection devices, and incidental materials and labour necessary to form a complete stay cable system to support the bridge structure in accordance with the design, the applicable standards, specifications and/or special provisions.
The stay cables shall consist of the parallel strand system made up of parallel, individually polyethylene coated seven-wire strands, placed inside an external polyethylene stay pipe. The stay cable free length shall provide redundant protection against corrosion of the strands, by means of two complementary, nested barriers:
- The first barrier (or internal barrier) shall be a hot dip galvanic coating applied directly to the strand, and must cover the full length of the cable without a break.
- The second barrier (or external barrier) consists of an outer envelope and an intermediate medium between the outer envelope and the internal barrier. To prevent the internal barrier being consumed, the external barrier must be completely airtight, watertight and qualified as a corrosion barrier and shall remain intact between the end anchorages, or throughout the free length, transition areas and through the pylon saddle.
In addition, the intermediate medium must prevent any water or moisture that might get inside the external barrier from reaching the internal barrier.
The aerodynamic stability of the stay cable, in case of rainy wind, shall be assured by stay pipe surfacing. The resistance of the stay pipe to environmental aggression (thermal variation, mechanical attack, UV radiation and stress cracking) shall be ensured by a stay pipe with a thermal expansion range and an adequate formulation, as well as a transition and/or anti-vandalism tube in the bottom anchorage zone.
Internal corrosion barrier
The internal barrier of the stay cable shall be enhanced with a hot-dip coating of the seven-wire strands. To prevent the galvanization process from resulting in the reduction of the elastic limit, and to ensure a smooth outer surface of the wires, the coating shall be applied on the wires before the final drawing operation. The coating of the constituent wires of the strand shall be done before stranding.
The coating shall consist of pure zinc (galvanization) grade Z2 with a minimum of 99.95 per cent purity, as defined in BS EN 1179. The mass of zinc coating per area shall be between 190 and 350 g/m2 (average thickness between 26 urn and 49 urn). The coating thickness shall be uniform (without drops or local thickenings). The adhesive strength of the coating shall be verified by winding at last six whorls of one of the constituents of the coated strand, on a cylindrical mandrel. After the winding test, the whorls shall not present exfoliations or cracks.
The continuity of the coating shall be such that the test sample shall not exhibit, at any point located farther than 25 mm of the immersed end, a bright and adhesive layer of salmon-coloured copper which indicates bare steel at this location.
External corrosion barrier
The external barrier shall consist of a high-density polyethylene sheath extruded directly onto the strand, previously coated and filled with petroleum wax. The individual HDPE sheaths shall be made of high density black polyethylene classified PE 80 or more.
Individual HDPE Sheath
The material used shall be free of recycled materials. The extruded sheath shall comply with the following physical and mechanical specifications:
The thickness of the individual HDPE sheaths shall be greater than 1.5 mm, and the outer diameter of sheathed seven-wire strands shall be less than 19.5 mm. The use of thinner HDPE (not lower than 1.2mm) is permitted solely if special installation procedures are implemented to mitigate the risk of mechanical aggression on the HDPE sheath. Experience of previous successful implementation of such procedures shall be provided.
Petroleum wax filler
For standard PSS monostrand stay strand, the intermediate space among the wires and between the wires and the individual sheath of each strands, shall be filled with microcrystalline wax i.e. a malleable crystallised solid consisting of saturated hydrocarbons which are injected in a liquid state.
In any case, the void filler shall not comprise grease, to prevent problems of thermal stability and bleed. Due to the cracking hazard and the potential fretting fatigue, cement grout shall not be used as a void filler material.
The void filler material shall be injected in the workshop of the strand extrusion facility. The manufacturing process must completely fill the internal voids between the constituent wires of the strand and the voids between the wires and the individual sheath. Moreover, this process shall ensure that no voids will appear in the intermediate medium, due to thermal shrinkage, creep, setting or ageing of the void filler.
The filling material shall be continuous and durably stable. The weight of filler per unit length shall be between 5 and 12 g/m. For individually sheathed strands, the weighting procedure consists of comparing weights of a factory-made strand length before and after cleaning and de-waxing the wires and the HPDE sheath which has been cut longitudinally to allow the operations.
For applications where saddles are used for stays continuous through the towers, an alternative filler material can be required to enable force transfer from the strand through the internal corrosion barrier and into the saddle. In such cases the ability to transfer the shear and compressive loads from the strand to the saddle must be demonstrated to be sufficient to avoid sliding of the strand relative to the saddle, to avoid movement/creep of the strand relative to the internal corrosion barrier and without damaging the internal corrosion barrier. For satisfactory bond transfer the filler compound shall have the capacity to transfer minimum shear strength of 4 MPa at 20°C. The flexibility of the medium prevents the cracking of the corrosion barrier in the deviation area.
Sheathed strand
The bond of the sheath shall ensure a continuous protection of the steel despite the extreme thermal loading to which it might be subject throughout the lifetime of the project. Specifically, no shattering or cracking of the sheathing shall occur except at the impact area.
The outer casing shall consist of a one-piece stay pipe through which the strands are threaded. The void within this outer casing shall not be filled. The characteristics of the outer casing, especially its thickness and chemical composition, must ensure good ageing performance against environmental degradation including satisfactory resistance to ultraviolet radiation. The colour of the outer casing shall be as per the engineer requirements provided the impact on durability is evaluated and proven satisfactory. The project specifications shall state the type of duct required for the project out of the three available duct diameters: Standard, Compact or Super Compact.
High density polyethylene pipe
HDPE stay pipe shall consist of a co-extruded high-density polyethylene, with a coloured external layer and a black internal layer. Stay pipe shall be made of high density polyethylene classified PE 325443 C (equivalent to PE 80 or PE 100).
Resistance to the environment of the outer casing shall be demonstrated scientifically: the outer casing shall be formulated for a pre-defined lifetime, which shall be backed by results of accelerated aging tests in SEPAP 12.24 cells. This lifetime under a climate equivalent to a solar intensity of 5 GJoule/m2/year (120kLy/year) and 8 hours per day sun exposure, shall be the following depending on the colour.
Anchorage
The two ends of a stay cable are called the anchorage zones. An anchorage zone consists of:
- The anchorage head i.e. the systems consisting chiefly of an intermediary mechanical part designed to secure the strands of the cable and transmit their force to the attaching parts of the structure (deck crossbeam, gussets, anchor box etc.);
- The transition zone, which extends from the anchorage head to the start of the free length of the stay cable (cable and protective barriers); the transition zone is where the strands fan out, and may comprise deviators, transverse guide systems, internal/external dampers, and sealing systems.
The proposed stay cable system shall be a proven solution, with a record of successful full-scale system test programme(s) and in use for several years on at least 10 bridges with spans exceeding 300m.
Stay cable anchorages shall be designed to individually anchor each strand by a reversible means. Hard material (resin) filling or cement grouting shall not be allowed in the anchorage area. The anchorage device shall be capable of transmitting the full ultimate tensile force of the cable.
Guide deviators placed in the transition area to provide a fixed point to avoid deviation induced bending stresses from reaching the anchorage and imposing a transverse force on the structure ahead of the stay anchorage in the above cases, are not allowed. Any device placed to dampen the cable shall not be a substitute for the deviator.
Protection against corrosion
The two complementary corrosion-protection barriers must extend continuously through the free length and entire transition zones. If the external anti-corrosion barrier is replaced by a local casing in the anchorage, it must be injected with an appropriate blocking medium. This blocking medium shall be a flexible material. Hard material (resin) filling or cement grout shall not be allowed in the anchorage zone. At the end of the stay cable, the outer casing shall be closed with a watertight cap attached to the anchorage head and covering at least the entire area of the strand terminations. This cap shall be removable for inspection of the strand terminations.
This integrity and continuity of the waterproofing must be consistent with the other functions of the anchorage and maintained under all service conditions (vibration, movement, ageing, temperature variations etc.). The anchorage shall include a tightening system enabling adjustment or re-instatement of the waterproofing of the seals during the service life of the bridge.
The water-tightness at the entrance of the strand into the anchorage is a key factor. If the water-tightness is provided by an O-ring seal or neoprene sleeve, the waterproofing test shall be done with material which has been pre-aged with exposure to relevant ozone, oxygen, stress, IR and UV simulating the design life of the stay.
The sealing of the anchorage should not rely on the elastic performance of rubber or elastomeric or plastic sealing which can lose their elasticity over years, but on an active pressure in the sealing material not lower than 20 bars.
Protection against wear
To prevent fretting corrosion and fatigue, no steel to steel contact between the strand and the parts of the transition zone shall be allowed. Steps must be taken to prevent fretting corrosion and fatigue at critical points: at each deviation of the strand, where the strand enters the anchorage head etc. Cement grout filling or resin filling of any part of the anchorage is not permitted.
Removability
Anchorage design must allow for cable replacement with limited impact on traffic.
Cable stay saddles
Saddles shall be designed to provide continuity of the strands through the pylon and individually anchor each strand by a reversible mean. The strand load transfer capacity across the saddle shall be sufficient to prevent strand slipping under any load case (SLS, ULS, accidental loads). The adopted friction coefficient value shall be evidenced through tests performed on the saddle system, with radiuses and deviations relevant for the project.
The strands must be protected against corrosion by means of either extending the internal corrosion-protection barrier of the free length through the entire saddle zone, or by alternative means, when the strand is introduced in the saddle with its continuous double barrier corrosion protection, which can be composed of two different systems along the strand. The double barrier shall not reconstitute in the saddle after the threading of the strand into the saddle.
To prevent fretting corrosion and fretting fatigue, no steel to steel or steel to concrete/mortar contact between the strand wires and any part of the saddle shall be allowed.
The water-tightness at the entrance of the strand into the anchorage is a key factor. If the water-tightness is provided by an O ring seal or by a neoprene sleeve, the waterproofing test shall be done with material which has been pre-aged with a relevant ozone, oxygen, stress, IR and UV exposition simulating the design life of the stay.
Stay cable components shall be protected from corrosion, heat, abrasion and other harmful effects throughout the fabrication, shipping, delivery, storage and installation.
Fully Assembled Stay Cable
Qualification of the stay cable system is based on the following tests on the fully assembled cable:
- Three fatigue and ultimate strength tests, on representative units of the bridge, unless evidence of previous tests is submitted and accepted by the Engineer;
- One water-tightness test, on a reduced unit, unless evidence of previous test is submitted and accepted by the Engineer.
The specimen assemblies shall be tested by a recognised independent testing laboratory approved by the Engineer. The Engineer shall be notified a minimum of 30 days in advance of any fabrication or testing so that a representative of the Engineer may be present when the respective work is being performed.
All test data and results shall be submitted to the Engineer. Fabrication of anchors and cables shall not begin until the required tests (or previous test reports) are successfully completed (submitted) and written approval is given by the Engineer.
Acceptance of prior tests of stay cables
A reference of a fatigue test and a water-tightness test passed successfully as per above specifications shall be submitted to the Engineer at the tender stage.
Any previous test, conducted for a previous project as per the present specifications based on Chapter 11 of [1] on specimens similar to those recommended for this project, may be proposed to the Engineer as the basis for stay cable approval in lieu of the tests specified.
However, the quality control tests outlined must establish that the strands supplied for this project have geometrical, mechanical and fatigue characteristics equal to the ones used in the fatigue tests for the previous projects. Further, it must be demonstrated with shop drawings that the stay anchorage hardware proposed is the same as in the previous tests.
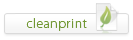
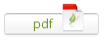
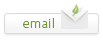