Nayan Bheda, Managing Director, Neptune Builders and Developers, describes precast technology as a modern tool for construction given the surging demand and increasing cost of labour and material.
To address the problem of lack of skilled labour and avoid delay in construction, the real estate industry has started looking for options to reduce production and construction cost. The answer to the industry’s dilemma is the concept of pre-engineered construction, the latest technology to hit the construction industry.
Also known as prefab or precast structures, this technology includes those buildings where the majority of structural components are standardised and produced in plants in a location away from the building, and then transported to the site for assembly.
These components are manufactured by industrial methods based on mass production in order to build a large number of buildings in a short time at low cost. The main features of this construction process are division and specialisation of human workforce, and use of tools, machinery, and other equipment, usually automated, in the production of standard, interchangeable parts and products.
Labour and material costs have increased by 20 per cent since 2010 and there is also a gap in demand and supply, hence this technology maintains highest levels of quality control as opposed to onsite pouring of concrete where temperature, humidity, material quality and craftsmanship play an important role. Since it is produced in a precast plant, it can be properly cured and closely monitored by plant employees, so there are no issues of leakages or cracks, thus ensuring uniform quality and reducing the maintenance and foundation costs considerably.
In India, only 27 per cent of all industrial and institutional buildings are pre-engineered, while in the United States, more than 70 per cent of all construction in industrial and institutional segments is pre-engineered. In India, the hybrid precast technology is under implementation; however, builders use ‘Shuttering’ method for faster completion of technology. But in this kind of technology the structures assembled are made at the construction site itself unlike prefab which are ferried from the factory situated in a remote location and are installed onsite to complete the structure.
Precast structures do not require finishing, like plastering or wall putty. Though more expensive than the conventional method, precast helps put buildings together more quickly.
|
There are various advantages to precast structures some of which are given below:
Efficiency: Precast technology saves up to 50 per cent of construction time.
Low maintenance: Precast concrete produces products of the highest quality, where stringent quality control measures are adopted, so the usual post-construction problems like leakage or cracks can be avoided. Therefore, it requires little or no maintenance post-construction.
Weather resistance: Unlike other construction materials that can rust, rot or degrade in the presence of moisture, precast concrete actually gets stronger if the un-hydrated cement particles in it react with water, thus making it completely water-resistant.
Fire resistance: Fire resistance of precast structure is same as any conventional RCC structure (steel and cement are not flammable materials but both behave differently in case of fire. Steel tends to give away its strength and concrete starts turning into powder in very high temperatures). Hence, RCC structure, conventional or precast, has similar resistance in case of fire as the concrete offers protection to the steel inside it.
Durability: Using precast concrete improves construction quality and thus extends the lifecycle of buildings. Studies have shown that precast concrete products can provide a service life of more than 100 years.
According to recent industry figures, the market for such structures is growing at 10 per cent per annum over the past five years, compared with overall industry growth of 20 per cent. The overall size of this industry is Rs.2,000 crore of which Rs.500 crore comprises residential projects.
The biggest technical advantage is the elimination of most formwork and considerable reduction in onsite concreting and brick lying; hence, to cope up with the surging demand and increasing cost of labour and material, precast can be the solution and a feasible model of construction.
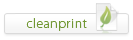
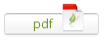
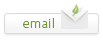