The pre-engineered building market is growing by 20 per cent per year. The continued growth of the market is assured as more and more companies adopting PEB systems, which have a huge potential in automobile, power, infrastructure and logistics segments, says Gautam Suri, CTO and Founder Director, Interarch Buildings Product Pvt. Ltd.
Pre-engineered metal building in India is not at a nascent stage anymore. The term and the sector both have been well accepted by India in the past two decades, though the process has been gradual but it has now received its due credit and importance. The PEB metal buildings have been proving its metal in several diverse sectors like automotives, public sector, oil and gas, power, retail, hospitals and hotels, to name a few.
With so many years into the construction sector, the technology was bound to undergo innovation and it certainly did. With the introduction of Light Gauge framing systems, green buildings, eco-friendly construction materials, options of so many possibilities with the metal buildings like multistory or high rises, multilevel car parks etc., the sector has seen variations and additions which have led the industry to where it is today.
Green buildings are steadily increasing their footprint in India. At present, there are already many buildings that have been officially recognised as green buildings, largely in the private sector. The Indian Green Building Council (IGBC) estimates the demand for green building materials and equipment will reach a billion dollar amount within the decade. The inclusion of better and more energy efficient buildings, conforming to international Green Building Standards and coders, greater use of reflective or thermal insulation, more natural lighting solutions via skylights and better ventilation in buildings using energy efficient vents, are some top of mind recall, talking of innovations that have set a benchmark in their own small ways.
In India, light gauge framing systems, have been contributing in construction of small buildings and homes in domestic and hilly areas.
PEB has a huge opportunity in automobile, power, infrastructure and logistics segments. It is the faster system to build infrastructure, to get the competitive edge in a newer business framework. More and more companies are adopting PEB systems and the PEB market is growing by 20 per cent per year. We foresee demand in the manufacturing and commercial sectors to increase by 50 per cent. The housing sector also should come up with similar demand.
Ten years down the line one will witness players from the organised sector serving the need (cost effectiveness, time saving and quality) of the customers in existing as well as some new sectors like power, bridges and highways, railways, metros, stadiums etc. These 10 years might also see a considerable shift of site fabrication work to the shop fabrication as the former eats away on time factor and quality. The industry will also witness more and more international market opportunities which will also add to the rise in demand of pre-engineered buildings. Hence, I feel that pre-engineered buildings in India will have a great future as it has in developed countries.
Case study
Interarch’s and Tata Motors association dates back to the 1990s, when Interarch started working with the company for roofing projects for its Pune facilities. Since then, over the last two decades, Interarch has been actively involved in completion of pre-engineered structures for many manufacturing units for Tata Motors across various locations in the country.
To increase its production capacity of light trucks and Marcopolo buses, which have strong demand in the market, Tata Motors set up a new project in Dharwad, Karnataka. The Ace was manufactured at the company’s Pantnagar plant in Uttarakhand, and the Dharwad plant will be the second facility for the light truck, after the production at Pantnagar reached full capacity.
Tata Motors wanted to construct this plant not only in record time to cater to the growing demand for mini trucks, but also wanted the state-of-the-art manufacturing facility to be built with green building norms. After completion, this was going to be the first green ‘greenfield automotive project’ in the history of the company and India.
The green manufacturing facility with numerous buildings like paint shop with four bays, engine shop, main plant building, administrative blocks etc., worth Rs.86 crore was awarded to Interarch. The plant is spread over an area of 72,000 sq. m. Interarch followed green features for the manufacturing facility keeping IGBC norms under consideration. These included:
- Low VOC paint to be used on buildings.
- All buildings to have white roof.
- Special glazing for windows with sun shed to meet IGBC norms.
- Ventilation system would be designed in a way as to help in proper air flow and temperature control thus providing healthy and comfortable indoor environment.
- Bare galvalume with sleep slope (>1:6); this minimises the heat island effect.
- Installed 3-5 per cent skylights on the roof of the total roof area of the building which reduces the need of artificial lights inside the building and saves electricity.
Interarch’s design department reduced the engineering time of the manufacturing plant which was very complex. The main building and the paint shop were designed using IS-1984 designed building structure norms with heavy collateral loading to meet all manufacturing and MEP support needs. The paint shop building was even more complex as there were multilevel mezzanines in the building with heavy collateral load for paint equipment installations and application provided by DURR with a lot of auxiliary structures to meet functional requirement.
KEY PROJECT HIGHLIGHTS
|
|
Project | Tata Motors Ltd |
Building Location | Dharwad, Karnataka |
Building Usage | Manufacturing facility |
No. of Buildings | 11 |
Tonnage of Building | 8,000 tonnes |
Roofing Supplied in MT | 83,000 sq. metres |
Value of Project | `86 crore |
Area of Project | 72,000 sq. metres |
Manpower Deployed | 500 |
Important Feature of Project | * Complete factory will designed and manufactured under the norms of Green Buildings* Multilevel mezzanines with heavy collateral load for paint equipment installations
* IS-1984 designed building structure with heavy collateral loading to meet all manufacturing and MEP support needs * Regular quality check and action jointly with client to achieve best quality in line with global standard * Site roll forming for entire roofing, cladding, liner etc. for faster manufacturing and quality control * Highest level of safety standard achieving zero accident with 500 semiskilled and unskilled labors at the peak time. |
The monsoon season and remote location of the site with a lean population in the nearby area along with the high safety standard required by Tata was a big challenge.
Interarch had to deploy innovative solutions like highest safety standard which were followed in line with the international standard and Tata Motors’ guideline to achieve zero accident, and logistics and warehousing control at site to meet site standard norms. Daily tool box meetings to review the site status and the way forward as well as regular quality checks jointly with the client were done, and corrective measures to achieve best quality in line with global standard were taken.
The entire manufacturing plant consumed more than 5,000 tonnes of steel, which was supplied by Interarch manufacturing facilities in a record time of less than four months.
Highest level of safety standard was showcased by Interarch Project Management team at the site, achieving zero accident with over 500 semi-skilled and unskilled labourers employed at the site during peak time.
To complete the projects in time and exceed the quality norms set by the client, Interarch did site roll forming for the entire roofing and cladding systems, liner etc. This helped in conserving time and the company was able to get an endless length of sheeting. The complete manufacturing plant along with the paint shop consumed more than 72,000 sq. m of roofing and cladding
Interarch’s ability to complete the project under strict safety and quality guidelines has made us the market leaders in the pre-engineered building sector.
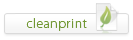
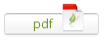
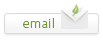
Thanks for sharing this post it’s really helpful to know about green buildings benefits and which way Real estate development companies involve in this projects thoroughly. I think number of Green buildings in Indiashould be increase.