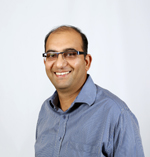
Head of Design
Emaar MGF
[metaslider id=9539]Pre-engineered buildings have a lot of advantages and some challenges that are being met successfully. A perfect plan is the essence of any system and PEB is all about proper planning. However, the most important step is to increase awareness amongst developers so that there can be a shift from conventional structures to PEBs. These structures use high quantity of recycled materials and save time and cost as only assembling of building materials are required at the project site, writes Rohit Mohan, Head of Design, Emaar MGF.
India is one of the fastest growing economies in the world. Apart from agriculture, the credit goes to the construction and manufacturing sector, as they are also driving the GDP and the overall economic system of the country. To support persistent development in the construction industry new technologies are evolving everyday and one of the novel concepts is pre-engineered buildings (PEBs). Contrary to the traditional onsite construction, PEBs are delivered as a complete finished product to the site from a single supplier with a basic structural steel framework attached with factory finished cladding and roofing components.
Prefabrication is an offsite manufacturing process that takes place in a specialised area in which various materials and building systems are joined to form a component or part of a larger final installation. Work is done at a remote location for increase in construction speed and quality. The type of prefabricated components varies, based on size and complexity and on the amount of labour required for onsite assembly.
PEB comprises structural system, sandwich panels, roofing, exterior facade and accessories. The concept is based on a design which usually involves a thorough project information data and details like building parameters, grade of steel, welding, anchor bolts, roof and wall liner/panel, insulation, sky light, gutters, facia, mezzanine, ridge ventilation etc.
Prefabricated building system consists of a series of integrated, carefully designed, factory-fabricated components. The typical prefabricated building system is composed of primary and secondary framing, roofing, wall, staircases and accessory subsystems which are manufactured to give the building versatility, stability, protection, performance predictability and lifecycle value.
Pre-engineered buildings can be of concrete, wooden or steel structure. In India, almost 27 per cent of institutional and industrial buildings are pre-engineered steel structures and awareness about them is increasing.
These days, architects are incorporating modern designs into the prefabricated houses. Prefab housing should not be compared to a mobile home in terms of appearance, but to that of a complex modern design. There has been an increase in the use of “green” materials in the construction of prefab houses. Since these homes are built in parts, it is easy for an owner to add additional rooms or even solar panels to the roofs. Many prefab houses can be customized to the specific location and climate, making it more flexible and modern.
The common examples of PEBs are ware houses, construction site offices, metro rail overhead track lines, flyovers, foot over bridges, hangers etc. Recently, a renowned contractor constructed first prefabricated high
4-stage: prefab construction process
* Design approval by the end user and any regulating authorities
* Assembly of module components in a controlled environment
* Transportation of modules to absolute destination
* Erection of modular units to form a finished building
Design
Repeatable design is a key benefit in prefab buildings. The consistent production process allows factory engineers and technicians to continually monitor the process and make improvements where ever possible to deliver the best product. Due to a controlled production environment, the latest manufacturing technologies and the design flexibility helps to produce high-quality (permanent or temporary) prefabricated buildings.
Also unique to prefab building is the ability to simultaneously construct a building’s floors, walls, ceilings, rafters and roofs. During conventional construction, walls cannot be set until floors are in position, and ceilings and rafters cannot be added until walls are erected. On the other hand, with modern modular methods of construction walls, floors, ceilings and rafters are all built at the same time, and then brought together in the same factory to form a building. This process brings modular construction time half to that of conventional, stick-built construction. Electrical wiring and plumbing are installed before the unit is ready for transport. Redundant quality controls confirm spot-on manufacturing accuracy before every prefabricated building part leaves the factory.
Assembling and onsite preparation
Modular construction takes multi-tasking to a whole new level. While the prefabricated building modules are built in the factory, the construction services professionals, on site prepare the foundation to receive the complete modules. The land is graded, cement foundation poured and piers are placed to support the complete prefab offices.
Transportation and erection
With all modules complete and shipped to the site, the foundation prepped and ready, the prefabricated modular buildings are set into place and connected to the foundation and each other for a solid and durable completed building. Utilities are connected and exterior finishes are added, perfectly matched to neighbouring buildings.
The resulting prefabricated modular buildings are environment-friendly, with the all the same architectural aesthetics, one would expect from conventional buildings.
Advantages of prefab
* Factory-control makes the best use of materials and produces less waste
* Reduced energy consumption compared to on-site construction
* Reduce disruption with offsite manufacturing and quick onsite modification
* More flexible in terms of design adjustments and modifications.
* Saves cost and time – requires less time in construction and fast to construct, if large number of units are identical
* Optimum use of materials
* High quality and superior finishing
* Construction operation less affected by weather
Disadvantages of prefab
* High initial capital cost
* Architectural design
* Improper connection of joints leads to error and water leakage
* Skilled labour is required
* Large volumes of similar units are required to be cost effective
* Few contractors/service providers
* Lack of awareness and market conditions
* Transportation and logistics
* Local bylaws and codes
PEBs have a lot of advantages and some challenges that are being met successfully. As it is said, a perfect plan is the essence of any system and PEB is all about proper planning. While planning, efforts should be made to reduce the number of parts, material and use lightweight elements to save on the transportation cost. However, the most important step is to increase the awareness amongst developers so that there can be a shift from conventional structures to PEBs. There are many ways to make the world green, which requires a mere shift in intention and commitment. With a well-deserved support, pre-engineered buildings promise a greener future ahead.
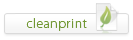
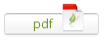
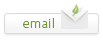
Other advantage : 1. Its Green Building concept
2. Require less manpower but skilled 3. Aesthetic view can be given
4. Earth quick resistant
5. it can provide low cost housing infrastructure for masses, which can fulfill housing requirement in Country like India.
6.Multistory building can be built with ease design and fabrication.
Sanjay Rana, Head- Business Development , M/s. Unicool Infra Systems