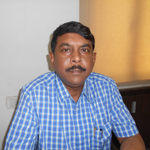
Assistant Vice President
CICO Technologies Ltd
Sukanta Mallik, Assistant Vice President, CICO Technologies Ltd, is hopeful that the slew of measures taken by the government to boost infrastructure development and stricter environment norms will put India’s anticorrosive material market on a sustained growth path, while making technological innovation a priority for industry players.
Corrosion is a cause of great concern for shipbuilding and construction industries globally. Not only does it impair functioning of structures in the long run, but could also cause a safety breach. Indirectly it also contributes to the depletion of natural resources. Infrastructure and related equipment in this sector are also made of steel, which in turn contains iron ore, a scarce natural resource.
Given that corrosion has no cure, prevention is the only available solution. The world over, and in India, protective coatings are used to help check corrosion. This segment, despite having significant future potential, registered small growth in the last few years due to an overall slowdown in the construction and infrastructure sector on the back of a subprime crisis. Now that stalled infrastructure projects, and the shipbuilding sector, are being revived, the demand for anticorrosion material products is also looking up.
Foreign suppliers have dominated the anticorrosive product segment in India despite the presence of a significant number of domestic suppliers, who are active regionally and benefit from longstanding customer relations. Construction chemicals’ manufacturers are attempting to stay on top of developments in the infrastructure and real estate sector, by investing in research and development to create innovative anticorrosive products which are easy to work with, and possess corrosion inhibiting features to prolong the life of metal. (Source: Wiki Commons)
In India, some of the anticorrosion products that have been in demand are epoxy, polyurethane, rich zinc primer, alkyd, fluorocarbon, acrylic, and chlorinated rubber. There has been a gradual shift towards higher quality epoxy and polyurethane coatings, recently.
Challenges
The Confederation of Indian Industry has estimated the impact of corrosion on the nation’s exchequer to be worth a staggering Rs.2 lakh crore. At least 25 per cent of the loss can be prevented by proper management. This, however, is not achieved in 75 per cent of the cases due to a knowledge gap. The industry does have the knowhow, but only in certain pockets. Losses due to corrosion in plants, machinery and equipment continue on a large scale. All stakeholders need to empower themselves to combat this problem.
Another challenge that the industry faces is the high annual cost of preventing corrosion, and difficulty in predicting this outlay, due to the varying degree of severity in practically all cases where metals and alloys are used. Anticorrosive chemicals, used in this sector, also pose the risk of injury, or loss of life, when handled at high temperatures and pressures, because they can make fairly harmless compounds explosive. Therefore, economising on construction materials is not an option. Proper monitoring of manufacturing facilities should be conducted by competent authorities to check against manufacturers flouting norms in this regard.
Strict environmental regulations on corrosion-resistant products are an area of concern for manufacturers. Norms depend on the location of the facility where these materials are used, and it is up to the participants to determine whether the systems comply with environmental regulations. The regulations are, however, leading to gradual shift in demand from epoxy-based anticorrosion coating (which is solvent-borne) to environmentally friendlier water-based acrylic anticorrosion coatings.
Opportunities
As per the report, ‘Anti-Corrosion Coating Market by Type (Epoxy, Polyurethane, Zinc, Alkyd, Acrylic), Technology (Solvent, Water, Powder), and End-Use (Marine, Oil & Gas, Power Generation, Industrial, Infrastructure, Automotive) — Global Trends & Forecasts to 2019,’ globally the anticorrosion coating market is projected to register a CAGR of 4.5 per cent between 2014 and 2019 to reach $26,583 million. We expect the segment to register close to double digit growth in India on the back of growth in power generation, infrastructure, automotive and transportation industries. (Source: Wiki Commons)
The huge financial and other losses caused due to corrosion, demand from its end-use industries, and technological development in the industry are the major drivers for the anticorrosion material market in India. Marine sector is also emerging as the largest end-use industry for anticorrosion coatings due to the government’s boost to the shipbuilding industry in India. We expect usage of advanced techniques in industries like oil and gas, and chemical processing, to boost the segment further.
Conclusion
India’s anticorrosive material market has witnessed growing demand in recent years due to increased activity in the industrial, infrastructure and shipbuilding sectors. An obstacle to market growth, however, lies in its highly raw material-intensive nature, making it vulnerable to fluctuations in the availability and price of raw materials.
We are hopeful that the slew of measures taken by the government to boost infrastructure development and stricter environment norms will put this segment on a sustained growth path while making technological innovation a priority for industry players.
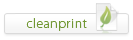
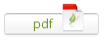
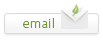