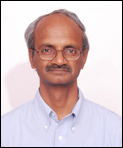
As the manufacturing sector embraces technology it is bound to change the way in which manufacturing businesses operate; it will also have an effect throughout the operating cycle – from product design, development, and supply chain management to distribution, says Ramesh Subramanian, Global Delivery Head, Blue Star Infotech.
Manufacturing is pivotal for economic progress of any country and in India it contributes about 16 per cent of our Gross Domestic Product. As India is poised to be a manufacturing hub primarily due to its growing domestic demand, with foreign players venturing into the Indian market, there will be great demand for both liquidity and talent. There is the vast domestic market with surging wages, as well as uncertainties and cost economics from global angles that guides this preference. Backed by policies and plans by the government India’s promise as a pivotal manufacturing destination have witnessed a massive upswing.
However, in order to remain competitive in the global arena, the Indian manufacturing sector has to really gear up as competition is intense and low-cost destinations are always around the next corner. Factors such as labour and capital productivity, infrastructure and environmental clearances are critical to the manufacturing sector, but the most significant is technology. Technology will play a major role to not only improve efficiency, productivity and quality but also cut costs and reduce material expenditure and energy consumption.
As the manufacturing sector embraces technology it is bound to change the way in which manufacturing businesses operate; it will also have an effect throughout the operating cycle – from product design, development, and supply chain management to distribution. Organisations have already started moving from legacy systems and most of them have adopted ERP (Enterprise Resource Planning). The challenge, however, is integration of IT and to train and enable an optimum man-machine interface which convinces management and employees to adopt new systems and processes and supports smooth rollout of the same.
Adoption of ERP in manufacturing has matured after decades of investment and all the departments from production and sales to operations and finance are connected by a common IT enabled platform, thus giving an integrated view of operations to the company’s management.
The emergence of new-age technologies, specifically SMAC, will further add to the transformation of the manufacturing sector. Here is a glimpse of how each technology will have its impact on manufacturing:
1. Cloud: Cloud will have greatest impact. With the Cloud, manufacturing units don’t have to set up their own infrastructure. The three core components of Cloud — Iaas, PaaS and SaaS — enables any manufacturing unit to adopt and use latest tools and technologies without wasting time and resources. Cloud can replicate similar IT services in manufacturing units spread across different geographies. Integrating IT in different units spread geographically used to be a big challenge earlier, but with the adoption of cloud, this issue to can be put to rest easily and at a very low cost.
Earlier, when setting up a unit in remote location, engineers would usually travel to, build the entire IT infrastructure, run it for months and then train the employees before finally handing over to the locals in factories. Now with Cloud, one can easily replicate the existing infrastructure in new plants and can make the system can be up and running with limited costs and resources.
Cloud adoption also enables the conversion of capital expenses in IT into an operational, and transaction-correlated operational expense. This, of course, leads to far greater agility than possible with own IT resources, not to mention the ability to focus better on operations rather than on IT.
2. Mobility: The adoption of mobility is still low within the manufacturing sector.
The impact would vary throughout the manufacturing value chain – product design and engineering may have a very low impact; sales, customer service and installation may have a very high impact.
Most enterprises are hesitant as the ROI from mobility is still not clearly established. Mobility just doesn’t mean providing mobile devices to employees, but entire ecosystem need to be build and integrated to get true benefits of mobility. This includes connecting shop floor to production department, inventory management and even with sales and customer service. This can enable real-time information flow throughout the supply chain, with production managers, sales team can get real time information about the inventory, can supervise the shop floor remotely. Though the benefits of mobility are clear in terms of reducing costs, bringing in efficiency and productivity, the challenges remain in terms of a clear cut strategy which can really work. There are multiple devices and platforms, and integrating them together as well as enabling machine to machine and man to machine communication would be a challenge.
The other challenge is to drive “consumption,” i.e. to derive meaningful usage of reports, statistics, workflows and analytics using the mobile platform, so that such details are always available with managers and decision-makers of the company at all times. As competition in the consumer market grows, and government policy and infrastructure turn into enablers rather than disablers, we should see the need for speed and agility come to fore, and result in a strong “pull” for such services in all manufacturing industries.
3. Analytics: Most manufacturing companies have already implemented ERP and BI tools. However, these remain restricted to basic information about sales, inventory, and purchase for the management, and are still not used for fact based decision making.
Advanced and predictive analytics can change new product development, efficiency in supply chain management and enhance customer relationships. Manufacturing units may have collated huge volumes of data over the years, which primarily remained unutilised. Analysing them can help to identify causes for supply chain inefficiencies, such as inventory pileups, machine failures, critical labour shortage etc. and enable mitigation in advance.
Product lifecycles have become shorter, so to stay competitive, enhancement of existing products and development of new products by understanding customer psyche is increasingly important. Analytics can help to understand the knowledge generated during developmental phase of a product and can help the product development team. Analytics can help to analyse customer data and thus develop a product which is more apt for the market. Adoption of analytics should increase for manufacturing sector with the increasing facilitative conditions for Indian manufacturing.
4. Social (Collaboration Tools): Such tools are yet to be employed by the manufacturing sector. Although companies have started using collaborative tools in the last few years, they are employed in a very ad-hoc way. Investment in social collaboration tools is not seen as priority right now for manufacturing sector, with the tradition of very few “knowledge workers” needing collaboration as opposed to administrators, blue collar workers and machines.
There have been specific collaboration tools in sectors of the manufacturing industry to ease communication flow in the supply chain, exchange large data files within specific teams, etc. However, using a truly “social” approach is as yet not on the radar. This will inevitably change with the introduction of more intelligence in the supply chain, in manufacturing processes, and disaggregation across the value chain, all of which would lead to a higher need for “social” collaboration as opposed to directive information-sharing.
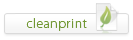
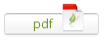
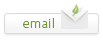